DfAM:从微型涡轮机外壳的设计来看功能集成一体化设计的未来
增材制造(Additive Manufacturing,AM)技术,是相对于传统的材料去除加工工艺而提出的通过材料逐层增加的方式直接制造零件的一类技术。与材料“去除法”相比,增材制造技术能有效缩短生产周期、降低制造成本,并且具有较高的柔性、适应性及材料利用率等特点。在航空航天、汽车、模具、医疗等不同行业领域的增材制造应用越来越普遍。
增材制造设计DfAM(Design for Additive Manufacturing)一种创建、优化或调整零件、组件或产品的形式和功能以充分利用增材制造工艺优势的方法,实现正向设计、按需制造的核心过程。
DfAM是一个复杂的课题,也是一个热门的研究领域。虽然基本概念很容易理解,但要掌握它们的实施可能具有挑战性。随着增材技术(和工程设计软件)的能力不断进步,先进的产品设计和实践工程案例也在不断发展。
传统的工业思维模式是系统分解、零件加工和组件装配的思维模式,如图1所示。把整车分解为系统,在把系统分解成独立的零部件;把系统分解的每个零部件都加工出来;把加工出来的零部件通过焊接、螺栓等连接方式组装成系统,系统在通过各种连接方式组装成整车。这样做的目的是为了能够快速批量化地把产品制造出来。

增材制造技术具有的不受传统工艺限制的特点,为高性能新产品研制带来了颠覆性的突破和革命性的创新,实现了先进设计与先进制造的完美融合。同时该技术更能大幅度缩短生产周期、降低制造成本、节省材料消耗和加工制造费用。
本案例是一个关于微型涡轮机关键部件外壳的功能集成一体化设计的过程。
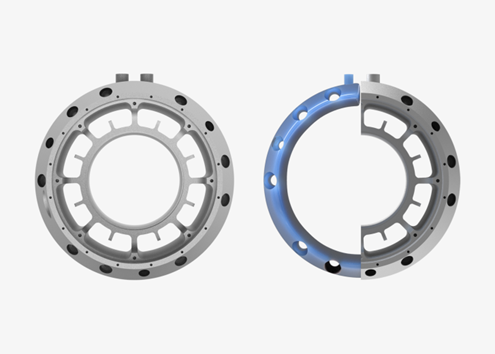
当发动机以90000rpm的速度旋转时,一切都需要精确对齐。装配中有多个零件会增加错位的机会。这样,零件整合是提高机器可靠性的一项重要技术。同时冷却系统是大功率能源发电系统的重要组成部分。事实上,热管理是电机的主要尺寸限制之一。简而言之,更好的冷却意味着更多的功率。
首先使用nTopology的集成静态和模态分析仿真工具确认外壳的壁厚设计,去除不必要的材料,创建一个可变壁厚的空心壳。
其次考虑到冷却散热的需求,通过模拟评估了随形冷却通道对系统性能的影响,nTopology中的热有限元分析结果与Fluent中的CFD仿真结果相结合。将热管理的随形冷却水道集成到整个外形壳上,形成具有用于冷却发动机和预热燃料的内部共形通道,这样的设计就把用于减重的中空结构用作冷却通道,完成了散热功能的集成。
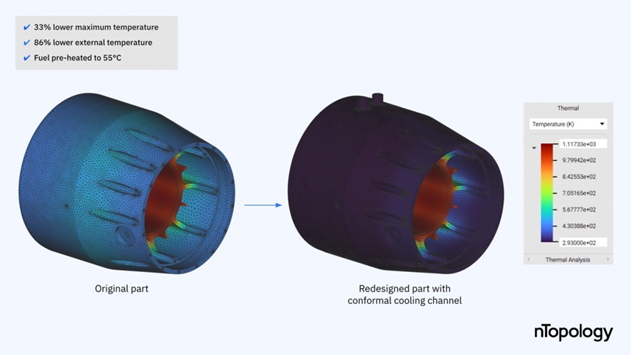
该部件实现了三种功能的集成,完成了一体化设计。并且整个结构的性能得到了大幅提升,部件的工作温度显着降低,最高温度降低了33%,而在发电机的外部温度下降了86%到27℃,使之可以安全触摸,同时整体减重44%。最后通过SLM成型工艺完成了整个结构的打印。
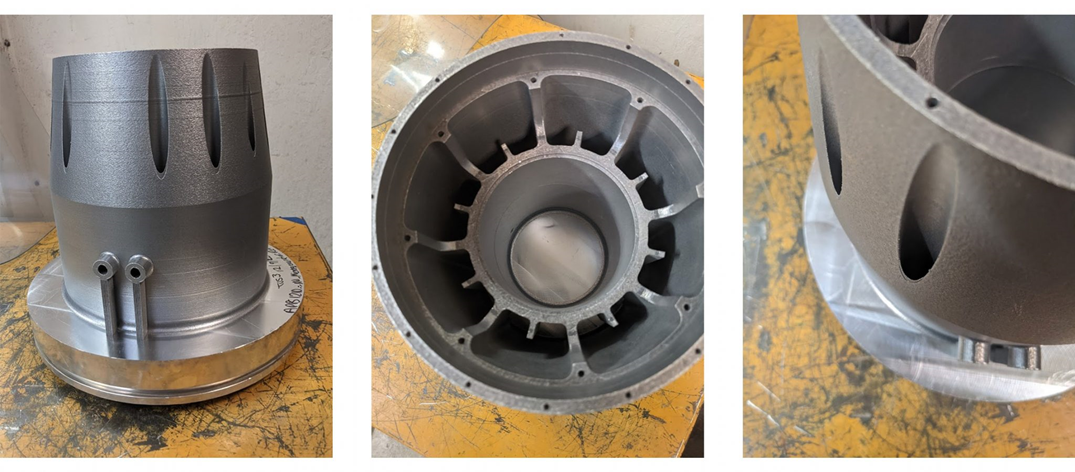
那么功能集成一体化设计就是在同一空间内实现不同功能结构材料与构型的相容,并且通过结构一体化实现轻量化,是对增材制造技术最直接的应用。从可靠性、轻量化角度出发,零部件是越少越好。比如实现结构-散热-气动或者结构-换热-减振等功能。
增材制造为通过将多种功能、多个部件组合成一个部件的打开了设计大门。当然,在进行功能集成一体化设计的过程中需要注意的几点:
-
取决于产品的设计空间;
-
产品与其他部件的装配关系;
-
加筋设计;
-
变厚度设计;
-
成型工艺;
-
制造设备的成型尺寸。
识别多部件一体化的机会具有挑战性。但考虑到好处时,值得付出努力。零件一体化可能导致:
-
通过消除对紧固件的需求来减轻重量;
-
降低装配和质量控制成本;
-
通过最小化潜在故障点的数量来提高可靠性。
增材制造技术可以实现复杂部件的一体化制造,这为零部件设计带来了优化的空间,设计师可以尝试将原本通过多个组件装配的复杂部件,进行一体化设计。这种方式不仅实现了零件的整体化结构,还能够避免原始多个零件组合时存在的连接结构(法兰、焊缝等),也可以帮助设计者突破束缚实现功能最优化设计。
增材制造将更精密的设计信息承载到物理实体上,意味着所生成制品具有更强的功能性,进而带来性能的飞跃。因此,在实现材尽其能、物尽其用,释放复杂成形能力的表象下,增材制造的真正价值在于回归设计本源,回归产品功能。
在航空航天制造领域,功能集成一体化设计的结构实现除了带来轻量化的优势,减少组装的需求也为航天航空发动机打开提升性能的想象空间。增材制造技术的这一优势受到了重视,并成为下一代航天航空研发发动机技术的抢滩高地。